Key Advantages and Considerations of Applying Plastic Extrusion in Your Jobs

Understanding the Basics of Plastic Extrusion
Plastic extrusion, a staple in the manufacturing sector, is a procedure that includes melting raw plastic material and reshaping it right into a constant account. This profile, once cooled down, can be reduced into desired lengths or curled for later use. The charm of plastic extrusion depends on its versatility. A variety of items, from piping to window structures, can be created. The process requires an extruder, a detailed maker with a heated barrel, a revolving screw, and a die at the end. The plastic product, in the form of pellets, is fed right into the extruder, where it's thawed and required via the die, taking its form. The choice of plastic and the layout of the die figure out the product's features.
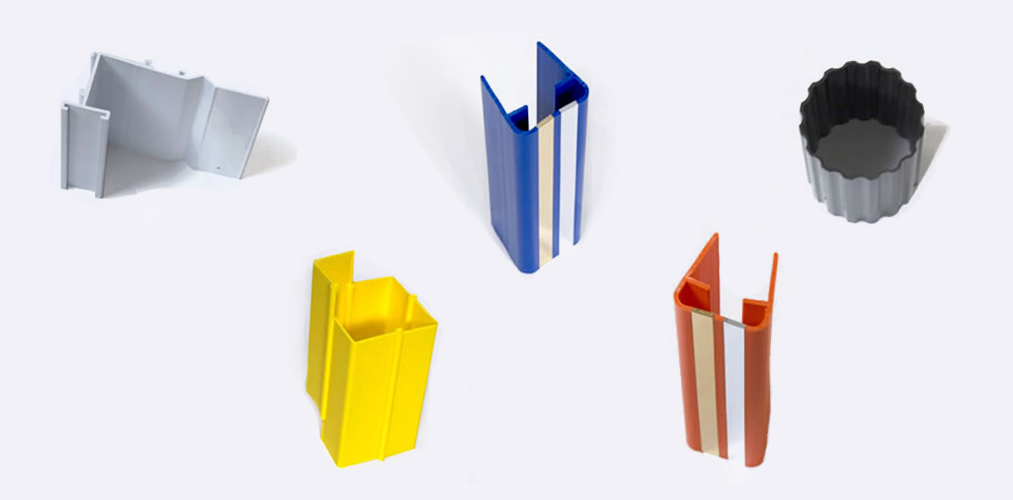
The Economic Advantage of Plastic Extrusion
The economic benefit of plastic extrusion lies mainly in 2 areas: economical product production and valuable production speeds. With plastic extrusion, organizations can produce high volumes of product at a reduced cost compared to various other approaches. The procedure flaunts a remarkable manufacturing speed, considerably minimizing time and more boosting its financial viability.
Affordable Material Production
A considerable advantage of plastic extrusion is its exceptional cost-effectiveness. This production procedure enables continual, high-volume manufacturing with very little waste, which converts right into reduced prices. The raw products utilized, commonly plastic pellets, are reasonably inexpensive compared to various other materials (plastic extrusion). The procedure itself calls for much less power than lots of various other production techniques, even more decreasing costs. Additionally, the extrusion procedure enables a high level of precision in forming the plastic, reducing the requirement for costly post-production alterations or corrections. Moreover, the resilience and longevity of extruded plastic items usually indicate less need for substitutes, adding to long-lasting savings. All these variables make plastic extrusion an extremely economical selection for lots of jobs, offering an eye-catching balance in between expense and performance.
Beneficial Production Speeds
While maintaining the cost-effectiveness of the materials, one more notable advantage of plastic extrusion lies in its rapid production speeds. This combination of rate, cost-effectiveness, and top quality highlights the considerable economic benefit of implementing plastic extrusion in numerous jobs.
Adaptability and Personalization: The Strengths of Plastic Extrusion
One of the noticeable staminas of plastic extrusion exists in its flexibility and customization possibility. These top qualities open the door to unlimited layout opportunities, providing manufacturers the capacity to tailor products to certain requirements. This heightened degree of customization not just improves item performance but additionally substantially boosts item uniqueness.
Unlimited Layout Possibilities
Plastic extrusion beams in its capability to offer nearly unlimited layout possibilities. This approach offers liberty to produce intricate shapes and detailed profiles, an accomplishment tough to achieve with various other fabrication methods. Owing to the liquid nature of molten plastic, the procedure is flexible enough to produce a diverse series of dimensions, kinds, and dimensions. The plastic can be adjusted to match unique specs, permitting the manufacturing of tailored geometries and meeting certain customer needs. Plastic extrusion can deal with a range of plastic types, increasing its application scope. This versatile strategy, therefore, serves a large range of industries from building to vehicle, product packaging to electronic devices, and past. With plastic extrusion, the design possibilities are practically limitless.
Enhancing Item Originality
The convenience of plastic extrusion can substantially boost item uniqueness. This process enables designers to experiment with different forms, dimensions, and shades, providing them the freedom to create unique items that attract attention in the market. It is this customization that offers a distinctive identity to each item, identifying it from its rivals.
Along with its aesthetic benefits, the customizability of plastic extrusion likewise offers practical advantages. Designers can modify the homes of the plastic according to the particular needs of the application, boosting the product's functionality. They can make the plastic a lot more versatile, extra sturdy, or much more resistant to warmth, depending on what the item needs. Thus, plastic extrusion not just boosts item individuality yet also its energy and marketability.
Layout Limitations in Plastic Extrusion: What You Need to Know
Just how can design restrictions possibly affect the procedure of plastic extrusion? While plastic extrusion is versatile, style constraints can curtail its advantages. Particular complex styles might not be viable because of the constraints of the extrusion procedure, potentially limiting the production of intricate profiles. The process is much less ideal for hollow or multi-chambered structures. In addition, the extrusion procedure may not always offer the preferred surface area coating, particularly for those needing high gloss or optical clearness. Product option can also position difficulties, as not all polymers are appropriate next page for extrusion. High-temperature immune plastics, for example, might offer difficulties. Comprehending these restrictions is critical for effective implementation of plastic extrusion in your projects. plastic extrusion.
Reviewing the Ecological Influence of Plastic Extrusion
While recognizing layout restrictions is a substantial element of plastic extrusion, it is similarly essential to consider its environmental implications. The Source process of plastic extrusion entails melting plastic products, possibly releasing hazardous gases into the environment. Better, the resulting items are commonly non-biodegradable, contributing to landfill waste. However, innovations in modern technology have actually enabled for more environmentally-friendly techniques. For circumstances, making use of recycled plastic materials in the extrusion process can lower environmental impact. Furthermore, developing eco-friendly plastic options can help minimize waste problems. Evaluating these ecological factors is critical when carrying out plastic extrusion projects, making certain a balance in between effectiveness, cost-effectiveness, and ecological obligation.
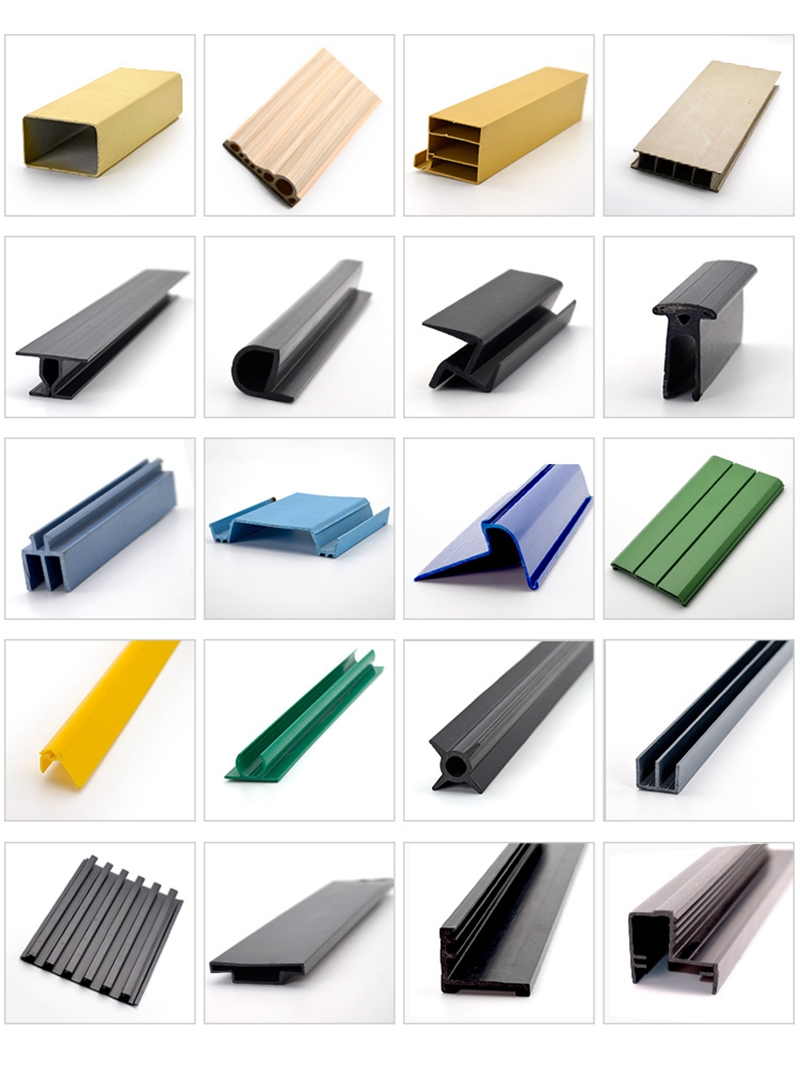
Instance Study: Successful Projects Utilizing Plastic Extrusion
Success stories in the area of plastic extrusion are plentiful, showing both the flexibility and effectiveness of this manufacturing process. plastic extrusion. One more effective instance is the manufacturing of plastic movie for product packaging and farming. These circumstances show plastic extrusion's important duty in numerous markets, attesting to its flexibility, cost-effectiveness, and trusted result.
Conclusion
To conclude, plastic extrusion offers a affordable and reliable technique for producing complex forms with very little waste. While it supplies numerous advantages such as cost-effectiveness and flexibility, it's critical to think about potential design restrictions and environmental effects. Executing recycled or biodegradable products can mitigate these issues, enhancing sustainability. Including plastic extrusion into jobs can lead to successful end results, as company website shown by numerous study.
Plastic extrusion, a staple in the production industry, is a process that involves melting raw plastic material and reshaping it into a continual profile. Plastic extrusion can manage a range of plastic types, increasing its application extent.Exactly how can make limitations possibly affect the procedure of plastic extrusion? The process of plastic extrusion includes melting plastic products, possibly releasing hazardous gases right into the setting. Using recycled plastic materials in the extrusion procedure can reduce environmental influence.
Comments on “Why plastic extrusion is ideal for mass production”